Written By: Roxanne Rose, Linamar Global Vice President of Human Resources
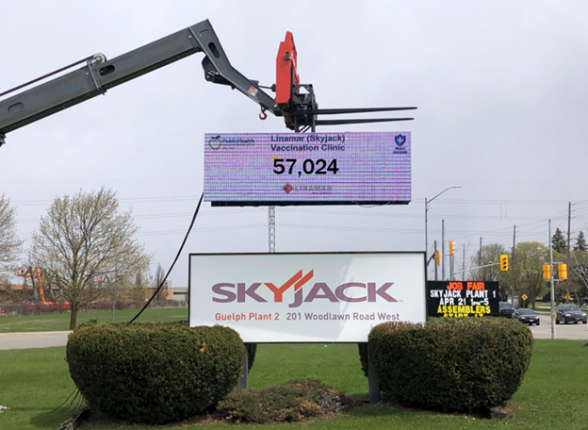
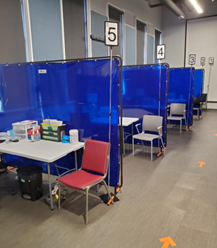

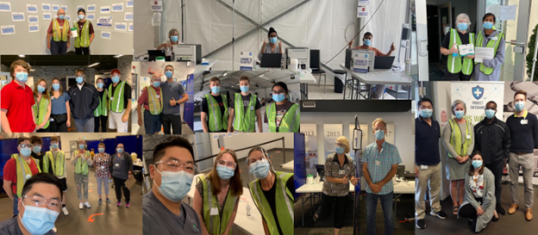
Well into our COVID-19 pandemic ‘New Normal’ we learned how to quickly adjust and adapt. At Linamar, we have guiding Leadership Behaviours and Values we attempt to instill in our employees. One of those behaviours is Responsiveness. The leadership value was originally meant to foster the fast pace, high-performance culture of our business that operates in a very demanding industry sector. But during the pandemic, it took on a new meaning of always “stay flexible, be ready to react and pivot if necessary.”
We were past the initial lockdowns, our customers and our own production lines had already come back online. We had implemented new policies intended to get back to work while ensuring our employees’ safety was at the center of everything we did. Linamar’s “Health First” task force met regularly to monitor, analyze and adapt wherever we needed to – not only within our own operations but within the broader community as well. Given our status as a major industry leader, a large employer, and a significant contributor to our local economy, the task force was also highly engaged with national, provincial, and local level officials. Having been consulted on the public policy for logistical planning and execution of the inevitable vaccine distribution to the general public, we recognized that we can play a big part there as well.
With our local Wellington-Dufferin-Guelph Public Health Unit, we began to plan for a Linamar Vaccine Clinic, located at one of our manufacturing sites. This was where we’d once again transfer our knowledge of project management, logistics, lean process flow, and high volume output not for auto part production, but for vaccinating the greater population. It was one of 5 temporary public mass vaccine sites that the health unit would set up. Entirely staffed, managed, and operated by Linamar we called our effort Project Safeguard.
- Over 57,000 doses administered
- 600 Linamar employees, Community Volunteers, and business leaders supporting the clinic
- As many as 1470 doses administered per day
- A Playbook for how to execute a similar clinic published and shared with the public for health units or private organizations looking to do the same thing
Again staying Responsive and being flexible was a definite asset as we neared the end of 2021. Months after we had closed our original Vaccine site, the Omicron wave of COVID-19 was coming. The team re-started a 3rd dose clinic on a smaller scale at a new site.
In my many years at Linamar, nothing comes close to the effort we put into our COVID-19 response. Project Safeguard is one that I’m incredibly proud of, a true example of “One Linamar” and way we can band together to solve nearly insurmountable problems.
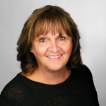
Roxanne Rose
Global Vice President of Human Resources