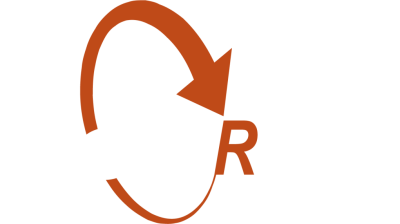
LinamaRadial
Our new radial machine combines the benefits of our existing high quality Hatebur blanks with the innovative radial forging process. This results in rotor shafts that not only stand out with regard to quality but are also extremely cost-effective. In addition to the rotor shafts, radial forging can also be used to produce a variety of other hollow and solid shafts for a wide spectrum of applications.
Benefits at a glance:
- Less production time
- Less resources
- Near-net-shape
- Cost savings
- Optimized environmental footprint
What’s the difference between just the single use of a radial forging machine?
Part of the finished rotor shaft is already produced in the pre-process on the Hatebur press. This area is not heated during radial forging and remains unchanged on the radially forged shaft. Only the area to be forged is partially heated and, uniquely, is radially forged in a single clamping operation. This slight technical difference to conventional technology significantly reduces the cycle time and has a positive cost effect. Through the near-net-shape production on our hot forging presses, we already have high material savings – perfect for further machining processes.